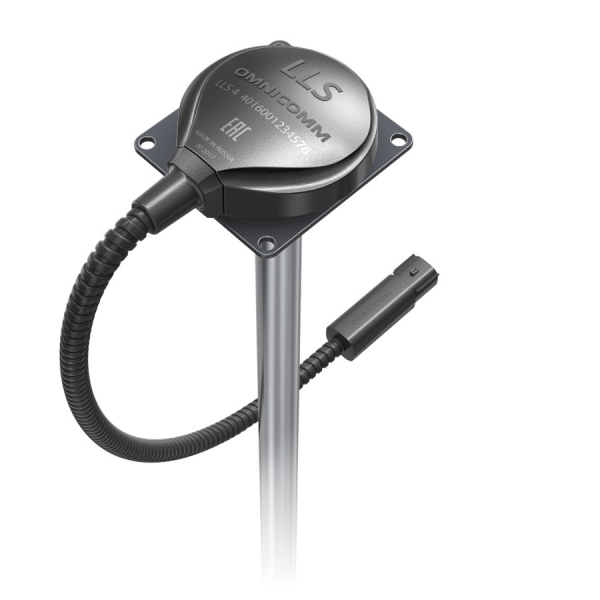
What are the Different Types of Fuel Level Sensors Used in Industries ?
Fuel level sensors are designed to monitor fuel levels in multiple types of vehicles, including locomotives, ships, and vessels. It can also be used to track the fuel level of stationary heavy equipment like generators and fuel station tanks. Rising fuel costs increasingly pushing fleet owners and asset managers to implement fuel monitoring technologies to effectively curb fuel-related expenditures. Fuel level sensors, in combination with IoT (Internet of Things) tracking and monitoring technologies, aid in the gathering of data including:
- Tank’s fuel level
- Fuel consumption rate
- Fuel refill/drain Status
- Analyze fuel theft/pilferage
- Check vehicle/asset idling time
Fuel Level Sensors and Their Different Types To monitor the real-time fuel level in tanks, different industries employ several types of fuel level sensors in the tank to monitor the volumes using the technology as per business requirements. In this post, we will go over the diverse types of industrial fuel level sensors that are employed, their functioning mechanism, sensor reliability, and sensor application in detail.
- Capacitive Fuel Level SensorsÂ
Capacitive level sensors are utilized for both point and continuous fuel level sensing. The capacitive fuel level sensor is the same as the capacitive liquid level sensor, which is used to detect oil levels. As the electrode’s height is regulated the fuel level between both electrodes’ changes, causing a dielectric shift, which causes a change in capacitance. Changes in oil level are converted into changes in capacitance value. Benefits of Capacitive Fuel Level Sensor
- They provide excellent precision, longevity, and dependability.
- Since there are no moving parts, the risk of wear and tear is eliminated.
- It can detect dense fuel and other fluids.
- Excellent sensitivity and outstanding accuracy.
- They can withstand turbulence.
Drawbacks of Capacitive Fuel Level Sensor
- It is extremely sensitive to changes in environmental variables like temperature and humidity. This will affect efficiency.
- Capacitance measurements are more difficult than resistance measurements.
- In comparison to inductive proximity sensors, capacitive proximity sensors are less reliable.
- The installation and calibration procedures are extremely complicated.
- Resistive/Float Fuel Level SensorÂ
These types of fuel sensors are mounted as standard in the fuel tank. The sensors are linked to a float, which travels up and down in response to the fuel level. As the float travels up and down, the sensor’s resistance shifts, leading to a change in output resistance and needle position in the gauge, and the resistance output and needle position alter with the current flowing across the coil. Benefits of Float Fuel Level Sensor
- Quick & Easy Installation
- Highly Affordable
- Demands Zero Maintenance
Drawbacks of Float Fuel Level Sensor
- Very Low accuracy of 80 to 85%
- Limited provision for installation
- Poor sensor operational lifetime
- Ultrasonic Fuel Level SensorsÂ
The ultrasonic level sensor monitors the fuel level using the ultrasonic wave concept. These are employed for non-contact continuous-level readings. A sensor (transducer) generates an ultrasonic signal, which is reflected from the liquid surface and then absorbed by the same sensor or ultrasonic receiver. The distance between the sensor and the liquid top surface is used to calculate the fuel/liquid level. The time between the transmission and reception of the ultrasonic wave is used to compute the volume of fuel in the tank. Benefits of Ultrasonic Fuel Level Sensor
- The design is simple, and the installation and maintenance are quick and easy.
- The measurement is accurate, consistent, and robust.
- The viscosity and density of the liquid have zero effect on the performance.
- Great sensitivity, high precision, and no maintenance are required because there are no moving components and zero contact sensing.
Drawbacks of Float Fuel Level Sensor
- The ultrasonic liquid sensing element has a blind area. A narrow region near the ultrasonic transducer cannot absorb ultrasonic pulses.
- Temperature and humidity have a significant impact on the ultrasonic liquid level measurement. The temperature change will produce a change in pulse wave speed, resulting in measurement inaccuracies.
- The dust has a major impact on ultrasonic liquid level gauges.
Why Fuel level sensors are important for your fleet business? A fuel monitoring and sensing solution can generate a strong ROI within months after installation. Fuel management software facilitates delivering comprehensive and precise data on fueling and draining activities. It lowers dependence on manual resources for fuel management, lowering overall fuel-related operational expenses. The key advantages of employing fuel level sensors include:
Delivers reliable and precise reporting on Fuel consumption and driving patterns.
Fuel savings can be accomplished by spotting illegal drains and eradicating pilferage.
Fuel management is an essential aspect of vehicle and machinery operations. For businesses and individuals reliant on transportation, having a reliable method to monitor fuel levels is crucial to prevent waste, improve operational efficiency, and ensure safety. This is where the fuel level sensor comes into play. In this blog post, we will explore what a fuel level sensor is, its role in fuel management, how it works, and its significance in various industries.
What is a Fuel Level Sensor?
A fuel level sensor is a device used to measure the amount of fuel in a vehicle’s fuel tank or storage tank. It is typically found in automobiles, trucks, boats, and industrial machinery, and it provides real-time data on fuel levels. The sensor is responsible for sending signals to the vehicle’s gauge or fleet management system, indicating the amount of fuel remaining in the tank. This allows drivers and fleet operators to monitor fuel levels and plan refueling efficiently.
Fuel level sensors play a crucial role in enhancing fuel efficiency, reducing costs, and preventing unexpected fuel shortages. They also help monitor fuel consumption, detect leaks, and maintain accurate data for operational and financial reporting.
How Do Fuel Level Sensors Work?
Fuel level sensors typically operate using one of the following technologies:
- Resistive Type Sensors: These are the most commonly used fuel level sensors. They consist of a float that rises and falls with the fuel level. Attached to the float is a resistive strip, which changes its resistance as the fuel level fluctuates. This change in resistance is then converted into an electrical signal, which is sent to the vehicle’s fuel gauge or an electronic control unit (ECU). The ECU or gauge uses this data to display the remaining fuel level.
- Capacitive Type Sensors: Capacitive sensors work by measuring the change in capacitance caused by the fuel level in the tank. These sensors have a pair of electrodes that create an electric field. When the fuel level changes, the capacitance between the electrodes alters, sending a signal to the monitoring system. Capacitive sensors are more accurate than resistive sensors and are often used in high-precision applications like aircraft and marine vessels.
- Ultrasonic Type Sensors: Ultrasonic sensors use sound waves to determine the fuel level. An ultrasonic pulse is emitted from the sensor, and the time it takes for the pulse to bounce back is measured. Based on this, the fuel level is calculated. These sensors do not have moving parts, making them more durable and reliable in harsh conditions.
- Optical Type Sensors: Optical fuel level sensors use infrared light to detect the fuel level. The sensor works by emitting light and measuring the amount of light reflected from the fuel’s surface. The more fuel in the tank, the less light is reflected back, and vice versa.
Key Features of Fuel Level Sensors
Modern fuel level sensors come with various features designed to enhance their performance, accuracy, and usability:
- Accuracy: High-quality sensors provide precise readings of fuel levels, ensuring that fuel consumption is accurately monitored and waste is minimized.
- Durability: Fuel level sensors are designed to withstand harsh environments. They are built with robust materials that can endure high temperatures, moisture, and vibration.
- Integration: Many fuel level sensors are designed to integrate seamlessly with other fleet management or telematics systems. This allows fleet operators to monitor fuel levels remotely and receive alerts in case of low fuel, fuel theft, or discrepancies in fuel usage.
- Leak Detection: Some advanced sensors include features that can detect fuel leaks. This is particularly useful for large-scale operations or in industries where fuel loss can be costly or hazardous.
- Maintenance Alerts: Fuel level sensors can also send alerts when maintenance is required, ensuring that the sensor remains in good working condition and continues to provide accurate data.
Applications of Fuel Level Sensors
Fuel level sensors are used across many industries and applications where fuel is stored or used. Here are a few key areas where these sensors play a critical role:
- Automotive Industry: In vehicles, fuel level sensors are integral to the fuel gauge system. These sensors ensure that drivers know when they need to refuel, preventing running out of fuel while driving. For commercial vehicles like trucks, fuel level sensors are also essential for fleet management, ensuring that fuel consumption is monitored and optimized.
- Maritime Industry: Boats and ships rely on accurate fuel monitoring to avoid running out of fuel in the middle of the water. Marine fuel level sensors are often equipped with additional features such as water detection to ensure that only fuel is being measured and not any water contamination.
- Aviation: Aircraft fuel systems use high-precision capacitive or resistive sensors to monitor fuel levels. Accurate fuel level measurement is vital for ensuring the safety and operational efficiency of flights, preventing fuel shortages or excessive fuel consumption.
- Agriculture: In agricultural machinery such as tractors and harvesters, fuel level sensors help monitor fuel usage during long working hours in remote areas. These sensors ensure that operators can plan refueling times efficiently and avoid delays in operations.
- Heavy Equipment: Construction, mining, and other industries that use heavy equipment benefit from fuel level sensors for managing fuel in their machinery. These sensors help track fuel consumption and optimize fleet operations.
Benefits of Using Fuel Level Sensors
- Improved Fuel Efficiency: By monitoring fuel levels in real-time, operators can optimize their fuel consumption, reduce waste, and minimize downtime caused by fuel shortages.
- Cost Savings: Accurate fuel monitoring helps prevent fuel theft, reduces unnecessary refueling, and ensures that vehicles or machinery are operating efficiently.
- Enhanced Safety: Fuel level sensors provide early warnings of low fuel or leaks, preventing potentially dangerous situations such as running out of fuel mid-operation or having a fuel spill.
- Environmental Benefits: By ensuring efficient fuel usage, fuel level sensors contribute to reducing the carbon footprint and improving sustainability.
- Remote Monitoring: With advanced sensors integrated into telematics systems, fleet managers can remotely monitor fuel levels across various locations, making it easier to manage large fleets and ensure optimal fuel usage.
Conclusion
Fuel level sensors are indispensable tools in the modern world of transportation, agriculture, and industry. They provide real-time data that helps manage fuel resources effectively, improving efficiency, reducing costs, and enhancing safety. Whether you’re operating a fleet of vehicles, a shipping vessel, or agricultural equipment, investing in a reliable fuel level sensor can make a significant difference in fuel management practices. As technology continues to evolve, these sensors are becoming even more accurate, efficient, and capable of offering more insights, helping industries optimize fuel usage like never before.
Add comment